Upgrading Boiler Room Efficiency
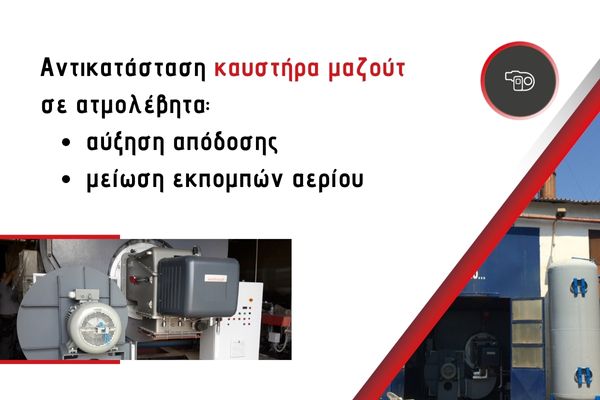
A leading consumer products company sought to improve the efficiency of its boiler room by upgrading its outdated burners.
The company reached out to KSA – Kalamarakis Automation for assistance in replacing the fuel oil burner of one of its steam boilers.
The need
The customer’s boiler room had 4 steam boilers with a capacity of 10-18tn/h and after a study, it was deemed necessary to upgrade the fuel oil burner of the 18tn/h steam boiler.
The existing burner had mechanical regulation components, leading to inaccuracies in fuel mixture control and high power consumption due to the lack of an inverter for the fan.
Additionally, sourcing spare parts for the aging burner was challenging, and the company faced a shortage of skilled personnel for maintenance due to retirements.
KSA proposal
As part of a recent project for a client, KSA Heating Systems proposed the installation of a new burner equipped with an electronic combustion control system and frequency converter to improve energy efficiency in multiple aspects.
The proposed solution included a modern 14,000kW WEISHAUPT fuel oil burner with a digital combustion system for improved accuracy in the mixture.
Additionally, an oxygen sensor with continuous control of exhaust gas quality was included to maintain the optimal oxygen percentage in the range of 2-2.5%.
This not only ensured more efficient operation but also reduced harmful emissions into the environment and resulted in fuel consumption savings of up to 2.5-3.5%.
To save electricity, a frequency converter–inverter was installed to provide variable RPM and noise reduction benefits, while also achieving energy savings of up to 60%.
Implementation
Following the acceptance of the detailed proposal, the project was implemented in collaboration with a specialized partner.
The implementation process involved the removal of the old burner, installation of the new equipment, and fine-tuning for optimal performance. KSA’s technical support and supply of spare parts ensured a smooth transition to the upgraded system:
On the 1st day, the old burner was removed & the steam boiler was cleaned. The workers also acquired a new fire structure before installing the new WEISHAUPT burner.
Day 2 and 3 included installing the boiler fan, adjusting the oxygen sensor as well as the frequency converter.
Then our partner took over the hydraulic and electrical connection of the burner, while the KSA technicians proceeded to ignite and put the burner into operation, at the same time making the oxygen adjustment for O2 trim operation
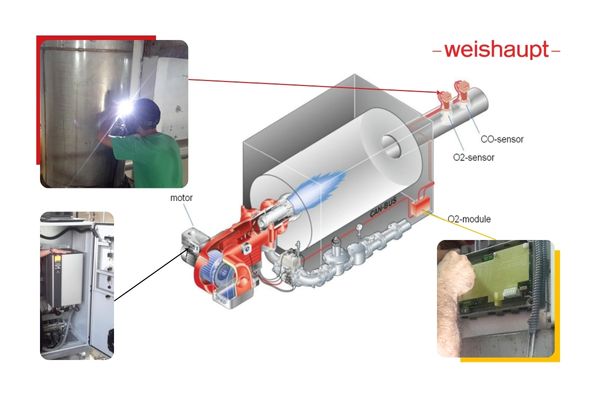
Benefits
- Technical Support from the KSA Heating Systems Team
- Full range of spare parts
- New, more efficient equipment with parts that save fuel & electricity
Conclusion
The results were evident, with improved efficiency, reduced emissions, and energy savings for the company. The project aligned with the Group’s goal of increasing global turnover while reducing its environmental impact, making it a successful partnership between the client and KSA.