BARILLA HELLAS: Energy Savings with Weishaupt burners
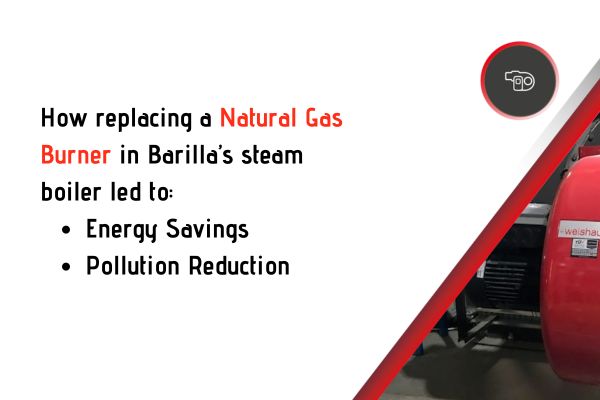
Barilla Hellas reached out to KALAMARAKIS AUTOMATION in 2016 in order to modernize the pasta production factory in Thiva, Greece, as part of efforts to promote sustainable development and enhance competitiveness.
The need
The factory had two superheated water boilers with a capacity of 9MW each, that were powered by outdated Natural Gas burners using mechanical operation. BARILLA aimed to reduce fuel and electricity costs, decrease NOx and CO2 emissions, and integrate the boiler-burner system with the plant’s BMS. The Energy department of KALAMARAKIS AUTOMATION was consulted to provide recommendations for meeting these objectives.
The solution
KALAMARAKIS AUTOMATION Energy Team first conducted a depreciation study, in order to offer a proposal tailored to the client’s needs and budget. This study involved installing a recorder in the boiler room to gather information on electricity and fuel consumption. The data collected is then inputted into Weishaupt’s “Efficiency Calculator” software, which provides a detailed analysis of depreciation including fuel costs in m3/h and €, as well as electricity costs in kWh and €.
Armed with specific data, the Energy team at KALAMARAKIS AUTOMATION put forth a proposal for the installation of a new WEISHAUPT burner equipped with an electronic combustion control system and frequency converter (inverter) to improve energy efficiency in three stages:
1. Weishaupt GmbH’s modern natural gas burner model WMG50/2-A
2.Addition of an Oxygen Sensor – O2 trim for enhanced efficiency, lowering fuel usage by 2.5-3.5% and minimizing harmful emissions
3. Integration of a Frequency Converter for variable rpm to reduce noise levels and decrease electricity costs by up to 60%, resulting in immediate savings on electricity bills
The team’s expertise and the customer’s past positive experience with Weishaupt burners made KALAMARAKIS AUTOMATION proposal a top priority due to its ability to meet all 3 of the customer’s needs.
Implementation
After accepting the offer, a specialized partner of KALAMARAKIS AUTOMATION went ahead with installing the new burner, making necessary adjustments to the boiler firing structure and natural gas network.
Subsequently, the Energy Team commissioned the WEISHAUPT Natural Gas burner, placed the O2 sensor in the chimney, and provided training sessions for the factory’s technical staff.
In 2022, this significant project’s completion involved installing thermal and electrical energy recording meters on all equipment.
This allowed the client to visualize and monitor energy usage online.
As a result, there was a 51,250m3 increase in fuel savings per year, a 5.1% decrease in electricity consumption, and further reduction in CO2 emissions
Benefits
The project brought numerous benefits to the industry.
Within less than 3 years, it enhanced the working conditions of factory technicians and enabled the monitoring and recording of combustion unit operations.
Additionally, the project resulted in significant fuel and electricity savings of 487MWh/year and 40.5MWh/year respectively, as well as a reduction in the industry’s environmental impact, with a decrease of 134.7t CO2 emissions and a 50% reduction in NOx emissions.
As a result of their efforts, both Barilla and the Energy Team of KALAMARAKIS AUTOMATION were honored with an Environmental Award in 2020 for their commitment to creating a sustainable environment and fostering economic growth within the Greek industry.